

Laser Blasting Pros
Learn More
Laser Cleaning works best on
Stone & Masonary

Limestone
Granite
Sandstone
Concrete
Brick
Marble
Terracotta
Laser cleaning is a highly effective method for restoring stone and masonry surfaces without using harsh chemicals or abrasive blasting. It gently removes soot, biological growth, paint, and surface stains from materials like brick, limestone, granite, and marble — all while preserving the integrity of the surface beneath. This makes it ideal for historic buildings, monuments, and delicate restoration projects where precision and care are essential.
Metal

Aluminum
Stainless steel
Mild steel
Brass
Copper
Tool steel
Titanium
Nickel alloys
Magnesium
Iron (cast Iron and wrought Iron
Laser cleaning is ideal for removing rust, paint, scale, and surface contaminants from a wide range of metals without damaging the material underneath. Whether it's steel, aluminum, copper, brass, cast iron, or stainless steel, the laser targets only the unwanted layer — leaving the base metal intact and ready for coating, welding, or inspection. It's precise, non-contact, and perfect for delicate components or high-value surfaces where traditional blasting would be too aggressive.
Painted and coated surfaces

Anti corrosion coatings
Lead based paint
Protective Layers
High build epoxy
Paint
Anodizing
Phospate coatings
Reduce waste & save on encapsulation
By vaporising coatings you can reduce the volume of the coating by 75%, this is on top of eliminating abrasives and chemicals
Laser removal of coatings is an ideal solution for toxic coatings as the disposal costs are minimal. Laser cleaning can greatly reduce the requirement for encapsulation as we operate a high-quality extraction system.
Composite & Non-Metallic Materials
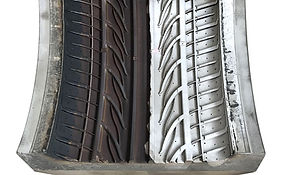
Carbon fiber (in some cases)
Fiberglass (non-abrasive removal of contaminants)
Plastics (high-heat resistance required)
Rubber (mold cleaning or prep)
Laser cleaning can be safely used on select composite and non-metallic materials when precise, non-contact surface preparation is required. It’s effective for removing release agents, light coatings, and contaminants from carbon fiber, fiberglass, certain plastics, and rubber molds — without damaging the substrate. With adjustable settings, the laser can be tuned to gently clean these sensitive surfaces, making it a valuable tool in industries like aerospace, manufacturing, and mold maintenance.
Other Materials
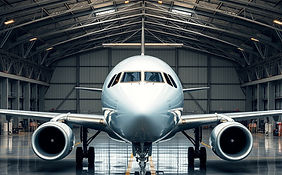
Wood ( varnish, lacquer soot/fire damage removal)
Glass molds (industrial application
Textured surfaces with corrosion or buildup
Rubber (mold cleaning or prep, depending on laser settings)
Delicate substrates like aerospace components or historic finishes
Laser cleaning is also effective on a variety of other materials where traditional methods may fall short. It can safely remove soot, adhesives, surface grime, and light coatings from surfaces like wood (with controlled settings), concrete, glass molds, and even painted signage. Because it’s non-abrasive and chemical-free, it’s an excellent option for specialty applications where maintaining the integrity of the surface is just as important as the cleaning itself.
What is laser cleaning, and how does it work?
Laser cleaning uses a focused beam of light to safely remove rust, paint, oil, and other contaminants from surfaces — without using abrasive materials, chemicals, or high-pressure blasting. The laser rapidly heats the surface layer, causing the unwanted material to break apart and lift off, while leaving the base material untouched.
Is it safe for the material underneath?
Yes. Laser cleaning is non-abrasive and non-destructive. It doesn’t grind, pit, or erode the base material. This makes it perfect for delicate or high-value surfaces — especially in aerospace, infrastructure, and historic restoration work.
How is it better than sandblasting or chemical stripping?
Laser cleaning:
-
Requires no media (no sand, no dry ice, no chemicals)
-
Creates no dust clouds or secondary waste
-
Requires minimal containment and cleanup
-
Is gentler and safer for sensitive surfaces
-
Is quieter and more operator-friendly
Sandblasting and chemicals have their place, but lasers are often the cleaner, safer, and more precise alternative — especially indoors or on high-value jobs.
Is laser cleaning eco-friendly?
Yes — it’s one of the greenest cleaning methods available. There are:
-
No chemicals or runoff
-
No spent media to collect and dispose of
-
Minimal power usage compared to large blasting systems
It’s safe for both the environment and the people working nearby.
What industries or projects is it best for?
Laser cleaning is a versatile solution used across a wide range of industries where precision, safety, and surface preservation are critical. It's ideal for:
-
Manufacturing & Industrial Maintenance – Equipment, molds, tools, prep and cleaning without downtime or disassembly.
-
Engineering & Fabrication – Weld prep, mill scale removal, and post-weld cleanup.
-
Maritime – Rust removal on ships, decks, pipes, and sensitive equipment without damaging surrounding materials.
-
Aviation – Cleaning delicate aerospace components without surface erosion or micro-cracks.
-
Rail – Surface prep, wheel and brake cleaning, and component restoration.
-
Fire Damage & Restoration – Soot, carbon, and paint removal on stone, brick, and metal after fire damage.
-
Historic Building Preservation – Stone and bronze restoration with no chemicals or abrasive media.
-
Oil & Gas – Cleaning pipelines, tanks, valves, and heat exchangers with minimal risk and fast setup.
-
Food Production Facilities – Non-contact cleaning of production machinery and components with no contamination risk.
Laser blasting is especially valuable when traditional methods like sandblasting, chemicals, or dry ice are too harsh, messy, or limited in precision.
Can it be done on-site?
Yes. Our system is fully mobile, allowing us to bring the laser directly to your jobsite — whether that’s a bridge, facility, warehouse, or restoration project. Quick setup and no media transport means we’re in and out faster, with less disruption.
What does it cost compared to traditional methods?
While laser cleaning equipment is more advanced, total job costs are often competitive or lower because there's:
-
No media to buy or dispose of
-
Less setup and containment
-
Minimal cleanup
-
Lower risk of surface damage or rework
For many projects, that translates to better long-term value.
How long does it take?
It depends on the surface and size of the job. Light surface rust may come off in seconds, while thicker coatings take longer. Laser cleaning is typically faster for prep work (since there's no masking, no cleanup), but slower on tough coatings like thick paint.
Is it loud or messy?
Laser cleaning is much quieter than sandblasting and doesn’t throw dust or debris into the air. It produces a faint popping or buzzing sound and a small amount of soot or residue that can be wiped or vacuumed. Most jobs require little to no cleanup.
Can laser cleaning remove deep rust or pitting?
Laser cleaning is highly effective on surface rust and oxidation. While it can clean into light pitting, it won’t fill or smooth out heavily corroded or eroded areas — it’s a cleaning process, not a resurfacing one.
Can you clean masonry or brick with a laser?
Yes! Laser cleaning is excellent for historic brick, limestone, granite, and marble, especially when traditional blasting would damage the surface. It’s commonly used in restoration of monuments, headstones, and historic buildings.
Does laser cleaning work on painted surfaces?
It can remove many types of paint, especially thinner or deteriorated coatings. However, very thick or industrial-grade paints (like automotive finishes) may take longer and might not be ideal for laser cleaning.
Can you clean equipment without disassembling it?
Yes — one of the biggest advantages of laser cleaning is that we can often clean machinery and parts in place, reducing downtime and labor. This makes it perfect for production lines or on-site maintenance.
Is laser cleaning safe after fire damage?
Yes. It’s ideal for removing soot, smoke residue, and char from stone, brick, and metal without spreading debris or damaging the surface. It’s also safer indoors than blasting or chemical stripping.
What kind of cleanup is required after laser cleaning?
Can laser cleaning remove oils or stains from concrete floors in manufacturing facilities?
Yes — laser cleaning is highly effective for removing oil, grease, surface grime, and light chemical stains from concrete floors commonly found in manufacturing and industrial settings. It cleans without water, chemicals, or blasting media, making it ideal for in-place cleaning with minimal disruption to ongoing operations. It's especially useful for maintenance zones, safety walkways, and prep areas where cleanliness is critical.
Can laser cleaning be used on wood, and what finishes can it remove?
Yes, laser cleaning can be used on wood, but it must be done with low power and extreme precision to avoid scorching or damaging the surface. It’s most effective for removing surface-level finishes such as:
-
Lacquer
-
Shellac
-
Varnish
-
Smoke damage and soot from fire restoration
-
Thin paint layers or old stains
It’s not recommended for thick, modern paint systems or pressure-treated lumber. We always perform a spot test first and adjust the laser’s settings carefully based on the wood type and condition.